metalworkingmag.de
22
'22
Written on Modified on
DMG MORI News
DMG MORI: WO TRADITIONELLE SCHLEIFPROZESSE AN IHRE GRENZEN STOSSEN, LEGT ULTRASONIC ERST RICHTIG LOS
Bis zur Jahrtausendwende galt das Innovationspotenzial der spanenden Bearbeitung als weitgehend ausgereizt. Nennenswerte Verbesserungen resultierten in der Regel vornehmlich aus dem Einsatz neuer Werkzeuge und Werkstoffe, schnelleren und „intelligenteren“ Parameteroptimierungen bzw. aus deren gezielter Abstimmungen auf einzelne Problemstellungen und Prozessgrößen mit Hilfe moderner Steuerungsgenerationen.
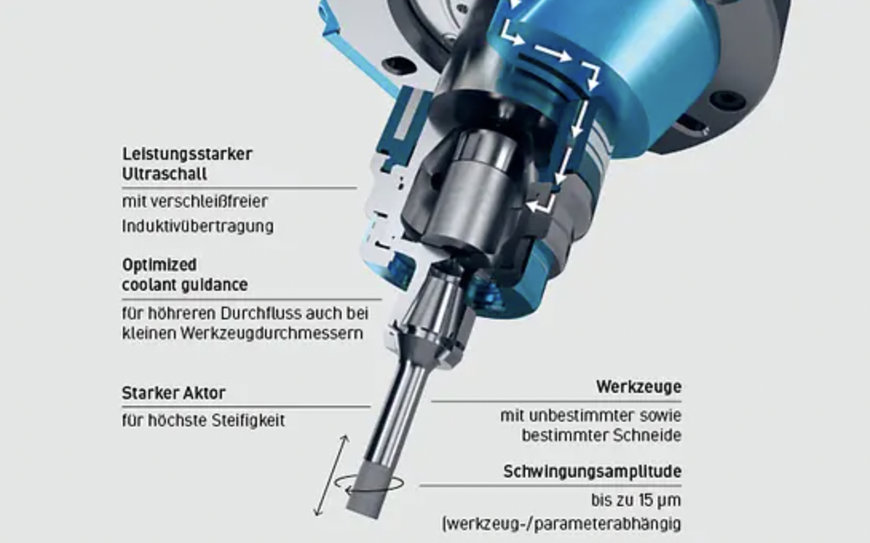
Ausgelöst worden war die Prozessevolution durch immer höher werdende Anforderungen in Folge neuer Werkstückmaterialien aus dem Umfeld der sogenannten „Advanced Materials“. Insbesondere gewannen dadurch frühere Entwicklungen an Bedeutung, die aufgrund ihrer geringen allgemeinen Relevanz bis dahin als Exoten gegolten hatten. Und eben dazu zählt die ultraschall-gestützte Materialbearbeitung, deren Ursprünge zwar bis in die 1950er-Jahre reichen, die aber erst gegen Ende des vergangenen Jahrhunderts zum industriellen Durchbruch ansetzte. Seit 2001 bereits gehört das ultraschall-gestützte Zerspanen zum Portfolio von DMG MORI, wo das Verfahren mit der Marke ULTRASONIC zum Programm erklärt wurde.
Schlagende Argumente
Im hybriden Kern der ultraschallgestützten Zerspanung geht es um eine simultane Überlagerung der Werkzeugrotation mit einer axial oszillierenden Bewegung im Hochfrequenzbereich als zusätzliche Wirkkomponente für den Materialabtrag. Experten sprechen hier vom piezoelektrischen Effekt, der genutzt wird, um Kleinstpartikel aus der Oberfläche des Werkstücks quasi „auszuschlagen“. Das klingt grob, ist jedoch im Ergebnis ein Materialabtrag allerfeinster Güte für die härtesten und bis dahin unzureichend ungelösten Aufgaben der spanenden Fertigungstechnik.
Das Erfolg bringenden Geheimnis hinter den Fähigkeiten des ULTRASONIC-Verfahrens ist insbesondere die Verringerung der vorherrschenden Prozesskräfte um bis zu 50 Prozent gegenüber konventionellen Bearbeitungsverfahren. Hierdurch lassen sich Vorschübe und Zustellungen erhöhen, Oberflächengüten verbessern oder der Werkzeugverschleiß minimieren – je nach Anforderung.
Das reduzierte einerseits die unmittelbaren Kosten, gewährleistete andererseits aber auch die für die industrielle Anwendung elementare Prozessqualität. Dazu addierte sich eine drastische Verringerung der Temperaturentwicklung an der Wirkstelle zwischen Werkzeug und Werkstück. Bislang als heikel geltende Materialien wie Keramik, Silizium oder Glas waren so plötzlich effizient bearbeitbar geworden. Hersteller von verschleißfreien Keramikbauteilen in der Textil- und Pumpenindustrie profitierten davon ebenso, wie die Bearbeiter von SiC, Quarzglas und Zerodur in der Optik-/ Halbleiterindustrie oder hochbeanspruchbarer Werkstoffkombinationen in der Luftfahrt- und Automobiltechnik.
Bald schon ließen sich auch mehrgliedrige Brücken, Stege und Implantate aus dem Dentalbereich mit den 3D-Daten des Originalzahns µm-genau als keramisches 1:1-Abbild in Passform bringen. Darüber hinaus gelangt es DMG MORI, das ULTRASONIC-Verfahren beispielsweise auch für Verbundstoffe, Hartmetall oder Korund, allesamt verschleiß- und korrosionsfest, druck-, form- und temperaturbeständig, zu erschließen.
Die bloße Grenzverschiebung in Richtung der „Advanced Materials“ war aber nicht allein ursächlich für den nachfolgenden Siegeszug. Dafür brauchte es zumindest noch eine weitere Zutat, nämlich höchste Präzision. Am besten veranschaulichen lässt sich dies unter anderem an den extremen Oberflächengüten von bis zu kleiner Ra 0,1 μm. Das heißt konkret, dass sich die Höhen- und Tiefenunterschiede über die gesamte Oberfläche eines Bauteils in einem Bereich von 0,1 µm bewegen. Bearbeitungsspuren sind in dieser Qualität für das menschliche Auge nicht mehr sichtbar.
Um die außergewöhnliche Präzision dennoch vermitteln zu können, hilft eine kurze Zwischenrechnung. 1 µm bzw. ein Mikrometer ist der millionste Teil eines Meters. Teilt man nun dieses Ergebnis durch 10, erhält man unter dem Strich die Oberflächenbeschaffenheit eines Bauteils nach der Ultrasonic-Bearbeitung.
Neben den exzellenten Eigenschaften bei Oberflächengüte und Maßhaltigkeit hat diese Präzision in Kombination mit den reduzierten Prozesskräften zudem Raum für neue Anwendungen geschaffen. Ein Beispiel ist der Einsatz von ULTRASONIC im Bereich der Halbleiterindustrie. Anwender aus diesem Technologiebereich wissen bereits seit mehr als 15 Jahren die „Ultraschall-Maschinen“ von DMG MORI in der Herstellung von Präzisionskomponenten aus technischer Keramik, Quarzglas oder auch Zerodur zu schätzen. Diese Werkstücke wiederum sind Schlüsselkomponenten, die in Lithographiesystemen zur Herstellung der immer leistungsfähigeren Mikrochips unerlässlich sind. Für dieses Branche wurde auch die neue Mikrobohrspindel ULTRASONIC MicroDrill entwickelt. Damit lassen sich - abhängig von Material und Prozessparametern – 10-tausende Bohrungen bis zu einem Durchmesser von lediglich 0,1 mm prozesssicher in Glas- und Keramikbauteile einbringen.
Als technologische Grundlage für diese feine Form der ULTRASONIC Bearbeitung „dient“ der umgekehrte piezoelektrische Effekt, unter dem sich beim Anlegen einer Spannung spezielle Piezoelemente ausdehnen bzw. zusammenziehen, was dem sogenannten ULTRASONIC-Aktor schließlich seine Kraft gibt. Konkret handelt es dabei um einen entsprechend aus- und aufgerüsteten HSK-Werkzeughalter, der dadurch in der Lage ist, eine hohe Amplitudenleistung von bis zu 15 µm zu gewährleisten. Eine weitere Besonderheit hierbei: Durch die ausschließliche Erzeugung mechanischer Schwingungen im Werkzeughalter kann die Werkzeugmaschine sowohl als Ultraschall- als auch als Standardmaschine eingesetzt werden. Zudem wird die benötigte elektrische Energie durch ein verschleißfreies induktives System übertragen, was eine volle Kompatibilität zu automatischen Werkzeugwechslern ermöglicht.
Das Bindeglied zwischen Spindel und Werkzeug gibt je nach Baugröße der Maschine in den Hohlschaftkegel-Ausführungen HSK-E32, HSK-E40, HSK-A63, HSK-A100. Der Hohlschaftkegel ist eine hochpräzise Weiterentwicklung des Steilkegels und bietet die perfekten Voraussetzung, die einzigartigen Vorteile des Verfahrens an die Wirkstelle zwischen ULTRASONIC-Werkzeug und Werkstück zu bringen.
Die neue Kompatibilität spiegelte sich bald in der gesteigerten Vielfalt des DMG MORI Portfolios wider. Neben einer Baureihe lupenreiner ULTRASONIC-Angebote lassen sich heute die meisten 5-Achs-Fräsmaschinen im DMG MORI Portfolio mit den imposanten ULTRASONIC-Fähigkeiten fertigungstechnisch aufrüsten. Das bearbeitbare Werkstückspektrum reicht dabei von Handtellerklein bis zur Großteilebearbeitung.
www.dmgmori.com
Fordern Sie weitere Informationen an…